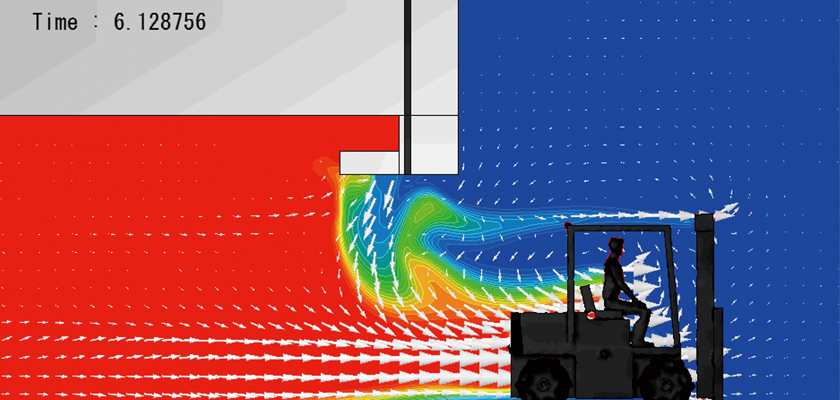
Case study: Developer
New order | Old order
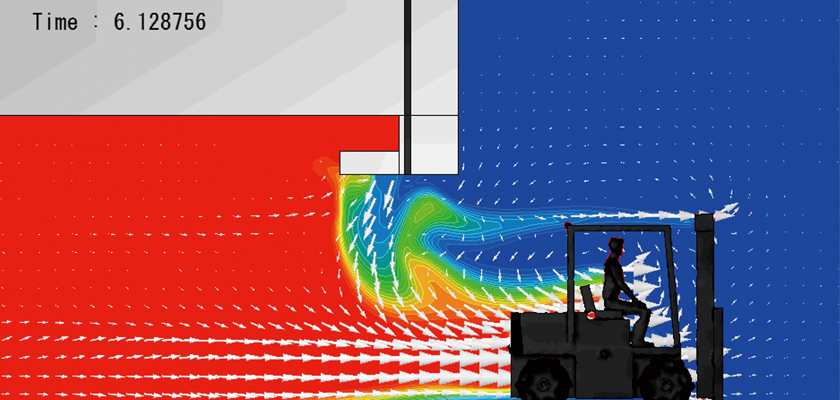
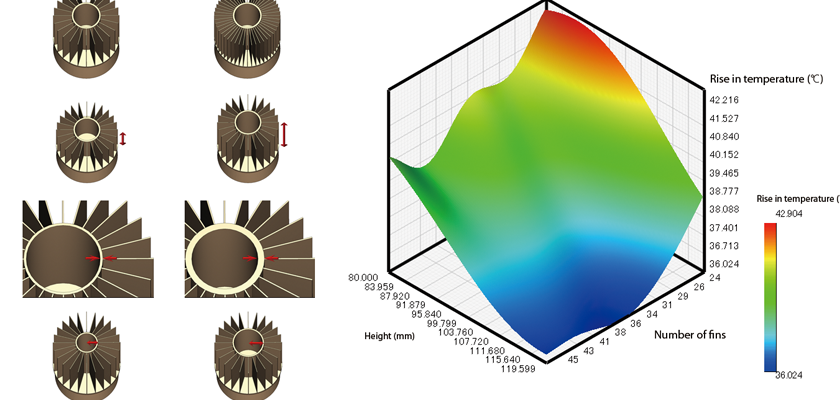
Optimization: Tool for Fast, Cost-Efficient Analysis

Thermoregulation Model JOS Function

Development of the Cavitating Flow Analysis Function
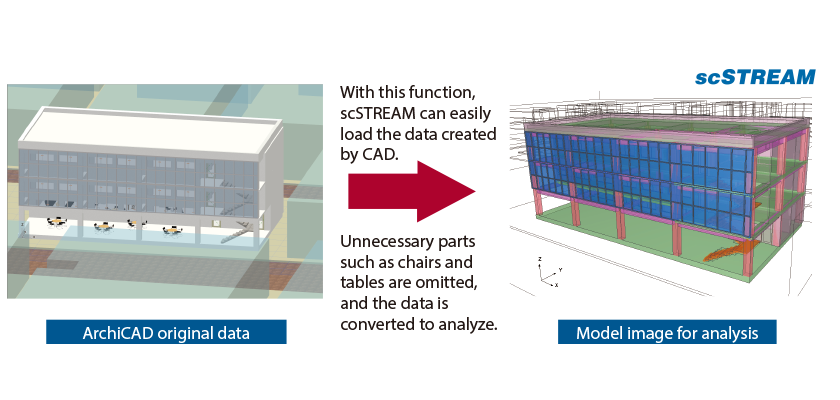
The Story Behind the Development of scSTREAM Launcher (Autodesk® Revit®) and Launcher (ARCHICAD)

Development of PICLS
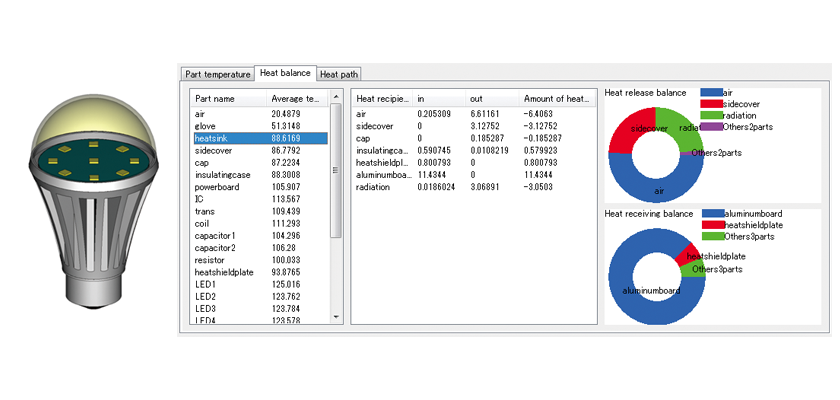
HeatPathView: Development Background
Picked Up Contents
Whitepaper
Turbocharging CFD with Katana
Unleashing cutting-edge computational fluid dynamics from Japan