TEN TECH LLC
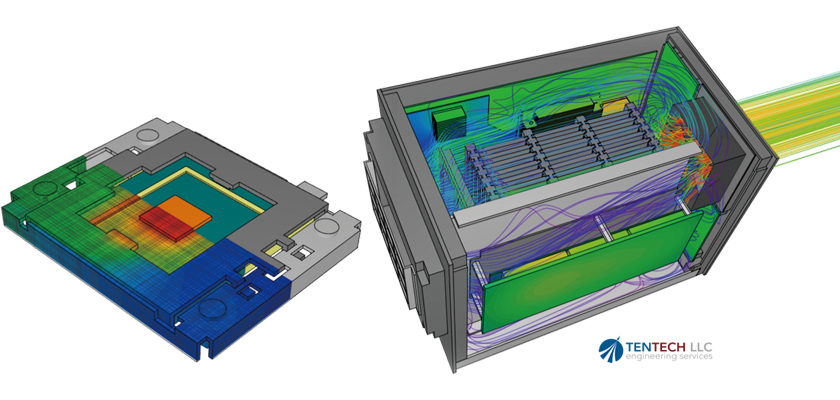
A Mechanical Engineering Consulting Company that Provides Design, Test and Analysis Services
TEN TECH LLC is an ITAR (International Traffic in Arms Regulations) registered mechanical engineering consulting company headquartered in Los Angeles, CA with operations in Billerica, MA, providing Mechanical Design, Analysis and Test services with emphasis on Aerospace & Defense, Hi-Tech Electronics and Renewable Energy applications. TEN TECH’s Mechanical Design Division specializes in Consumer-grade and Ruggedized Electro-Mechanical Packaging, Electromagnetic Interference Hardening and Plastic Parts Design. Its Mechanical Analysis Division provides expertise in Structural Dynamics, CFD (Computational Fluid Dynamics), Thermal Analysis, Vibro-acoustics and Aeroelasticity while the Physical Testing Division offers Shock & Vibration, Thermal, Acoustics, Salt/Fog, Humidity and Airflow testing services. TEN TECH has been one of Software Cradle’s power users since 2011.
Picture 1: William Villers, Co-founder and Director of Engineering at TEN TECH LLC
Mr. William Villers is a 25-year veteran of the aerospace and defense industry, with an ABD (All but dissertation) Doctorate in Mechanical Engineering from the Mediterranean Institute of Technology in Marseille, France. His expertise is in structural dynamics, shock, vibration, fluid dynamics and thermal analysis of mechanical systems, with a specialty in avionics systems and chassis. Working for major corporations including Eurocopter, Aerospatiale and EDS both in Europe and the United States, Mr. Villers has enjoyed a continuously growing and successful career in engineering and engineering management. Over the course of his career he has been part of and directed engineering activities for high-profile aerospace and defense programs including NH90, Ariane 5, JPL MER & MSL, and JSF to name a few. As a Managing Partner of TEN TECH LLC, his engineering knowledge and professional experiences are often called upon for Subject Matter Expert representation.
scSTREAM Met and Exceeded Expectations from Day 1
Meshing strategies can often be a key component that influences one’s decision on software. At least this was the case for TEN TECH as they were searching for Cartesian-grid coupled CFD/thermal software. There of course were more criteria in his mind: good geometry translators; geometry simplification capabilities; fast, accurate and sophisticated solver and post-processing; and yet competitive price. “scSTREAM met and exceeded all our expectations from day 1. It is extremely easy to use, very fast and very accurate at the same time.” Model handling and time constraint are a notorious issue when it comes to CFD analysis, but the modeling capability of the preprocessor and the solver speed of scSTREAM surprised him. “We are able to create accurate thermal models of complex systems in record time. We have used and evaluated several competitive products, one of which being the apparent de-facto standard, FloTHERM®. Not only was scSTREAM easier to use, had a better looking UI (user interface) and better performance, but the price was so much in favor of scSTREAM that our decision was very easy: scSTREAM has been our main CFD/thermal tool for the last 5 years for electronics cooling applications, and we have not regretted it.”
Just the Right Tool for Electronics Applications
Mr. Villers further discussed his company's success with scSTREAM for the last five years. “scSTREAM has been performing flawlessly for all of our electronics cooling applications: it is easy and fast to create a model, its solver is fast and accurate, and the ease and the quality of results and documentation are outstanding.” He pointed out that the visualization of the results is one of the strengths of scSTREAM: HeatPathView is a good example. Mr. Villers continued, “We have compared some of our thermal models with real test data and have found our analysis predictions to be within 5% of the test data for temperature and air flow. We have great confidence in the thermal predictions we make with scSTREAM.” He was happy to share two successful projects that his company has done.
Figure 1: Search & Rescue Radar System
Detailed Thermal Information Provided by HeatPathView
One of TEN TECH’s customers consulted for the feasibility of a radar processing system from a thermal management view. The initial analysis had been performed by the customer with FloTHERM®, but their resource was unavailable, and reproducing the geometry was inevitable. Mr. Villers recalls, “In a very short period of time, we were able to create an accurate thermal model from the 3D assembly, replicate the FloTHERM® model and add more design parameters to it to move the design study further along. We were able to create a more accurate model in half the time it took in FloTHERM®. In addition, thanks to advanced tools such as HeatPathView, we could gain better insight into the thermal performance of the system and improve the cooling path more efficiently.” HeatPathView integrated in scSTREAM is a supplementary tool that enables users to check the heat transfer among analysis parts, the directivity of the heat exchange, the form of heat transfer, as well as much detailed thermal information of each part. Figure 1 shows the search and rescue radar system model with the thermal information table and a graph that HeatPathView provides.
Figure 2: A detailed thermal model (left) and Ruggedized Data Recorder System model (right)
Accurately Predicting Device Performance in Harsh Environments
Another exciting work of TEN TECH to introduce is the entire cooling design of a military data recording and a storage unit. “As this system used COTS (commercial off-the-shelf) components, we had to create very detailed models to predict how consumer-grade electronics will operate in the harsh military environments,” said Mr. Villers. “With the help of scSTREAM’s high performance and efficient distributed computing system, we were able to quickly create very detailed models of over 20 million mesh elements, and perform many design verification and optimization iterations per day, including flow path optimization, fan sizing, heat sink optimization and placement.” The results are illustrated in the Figure 2: the Ruggedized Data Recorder System model (right) is shown with streamlines on which temperature contours are overlapped; and a detailed thermal model of the processor, Intel Xeon®, installed in the recorder unit (left) is shown half original model and half resultant temperature with mesh. As their analysis results obtained in scSTREAM showed an excellent correlation with predictions, the unit passed qualification testing with ease and is now operational on board the US Navy E-2D.
The Role of CFD Analysis in Electronics Industry
Mr. Villers stated that CFD analysis plays an essential role in the industry he is involved, from the feasibility test, conceptual design to final verification process. On the other hand, he also addressed the difficulties of conducting CFD in general: “Some of the harsh environments we have to deal with would be very impractical and costly to replicate in a test facility.” Of the most common issues discussed within this industry, including price-to-performance value, complexity of use, and quality of results interrogation and documentation, Mr. Villers explained how scSTREAM can alleviate most concerns. “scSTREAM addresses both price and performance points very well, and is constantly improving the user experience with the aesthetic appeal of the UI.” He said that the GUI (graphical user interface) is very important for “casual” users. He added that scSTREAM's ability to interrogate the model and visualize results in a clear and “pretty” manner is also on par with the best CFD software on the market.
Figure 3: Data Mapping with scSTREAM FLDUTIL
Future Usage of scSTREAM
Mr. Villers’ current work ranges widely from component-level to system level thermal analysis. The analysis with CFD greatly helps in the thermal management, design and qualification of defense electronics systems. Thanks to scSTREAM's versatility, TEN TECH sees an increased opportunity for CFD applications. “Future uses of scSTREAM will include building aerodynamics and air conditioning applications as well as Fluid Structure Interaction and CFD-FEA (Computational Fluid Dynamics-Finite Element Analysis) coupling, and/or co-simulation with Dassault Systèmes‘ Abaqus.” FLDUTIL, a supplementary tool of scSTREAM, enables the CFD results such as pressure information to be mapped into structural analysis tools like Abaqus. Figure 3 describes the connection between scSTREAM’s postprocessing file (FLD file) and structural analysis system. scSTREAM will continue to serve as a fast, simple, and reliable analysis tool for TEN TECH LLC.
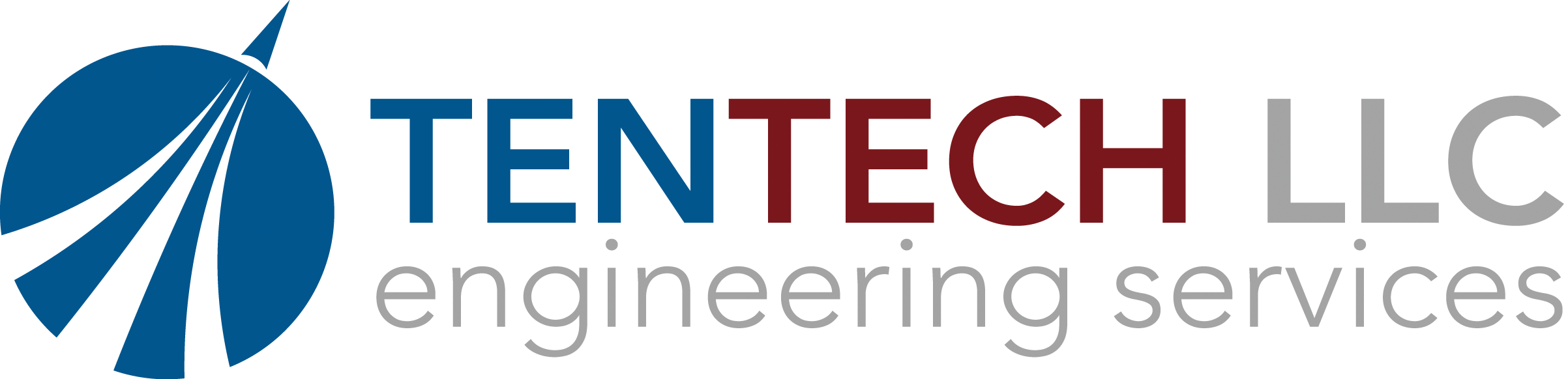
TEN TECH LLC
- Founded: 2011
- Business: Mechanical Engineering Consulting
- President: Connie Yokogawa
- Location: Los Angeles, CA (USA)
- Size: 10 - 50 employees
- URL: https://www.tentechllc.com
*All product and service names mentioned are registered trademarks or trademarks of their respective companies.
*Contents and specifications of products are as of January 31, 2016 and subject to change without notice. We shall not be held liable for any errors in figures and pictures, or any typographical errors.
Download