Nagoya Municipal Industrial Research Institute
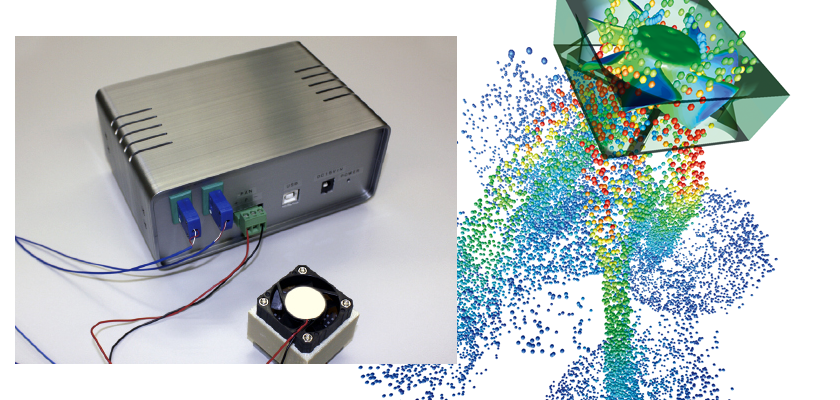
Helping Local Companies Solve Thermal Issues with CFD Tools
Nagoya Municipal Industrial Research Institute (NMIRI) is a public research institute in Nagoya city that provides test and analysis support to small/medium sized companies in cooperation with local industries. When the client's work involves thermal management, the engineers at NMIRI use Software Cradle simulation tools to perform the simulations. The engineers also use these tools for their own basic research and to verify the performance of test instrumentation.
(Left) Fig. 1 Nagoya Municipal Industrial Research Institute
(Right) Mr. Yasushi Kajita (Doctor of Engineering), System technology department, Production system laboratory, Nagoya Municipal Industrial Research Institute
NMIRI has been in operation since 1937. Over the years, it has demonstrated its value to local industries and established itself as a key contributor of test and analysis methods. A large part of the NMIRI portfolio is related to the automotive industry which has thrived in Nagoya. With a wide variety of measurement techniques and equipment, the institute has more than 80 engineers and is one of the largest public testing laboratories and research institutes in Japan. It specializes in three major areas of research: materials, electronics, and machinery. To encourage local companies to advance their technical capabilities, NMIRI provides technical support for no charge and also assists in conducting tests. They are also available to conduct joint research with their partners, while also providing classroom and on-site training.
Growing Demand for Thermal Management
NMIRI has also various analytical tools for structural and thermal-fluid analyses. Yasushi Kajita, a member of the NMIRI system technology department's production system laboratory, provides consultation and technical support for thermal management of electronic devices. Mr. Kajita is also responsible for resolving manufacturing mold thermal design issues that occur in the automotive industry.
Requests for assistance with thermal related issues have become more and more common at NMIRI. Electronics related inquiries account for 60-70% of Mr. Kajita's consultations. Most of the remaining inquiries deal with mechanical products such as mold cooling systems. Mr. Kajita primarily uses Cradle HeatDesigner thermal-fluid analysis software for electronics to perform his analyses. Although HeatDesigner is primarily designed for electronics, Mr. Kajita has also adapted its use for analyzing molds as well. HeatDesigner's ease of use, simplicity, and derivation from Cradle's scSTREAM general purpose, structured grid CFD software, made this adaptation by Mr. Kajita possible. Mr. Kajita performs the analyses himself, and encourages his clients to also use HeatDesigner.
NMIRI first started using CFD in 2005. Around this time, Mr. Kajita was also sensing the need to investigate the use of CFD because his clients were starting to explore the technology. Mr. Kajita felt that by developing in-depth knowledge and skill in CFD, he could provide greater value to NMIRI's partner companies. NMIRI uses the full range of Cradle CFD products, including SC/Tetra, scSTREAM, HeatDesigner, and CADthru. Mr. Kajita has developed his expertise with HeatDesigner and believes that its user-friendly operability for beginning users is one reason HeatDesigner is so popular. NMIRI primarily uses SC/Tetra for their basic research.
Fig. 2 Heat generation amount measurement system
Developing a System for Measuring the Amount of Heat Generation
One application where HeatDesigner plays a critical role is in the development of a system for measuring the amount of heat generation from electronic parts (Fig. 2). The system was developed in cooperation with SiM24 and the Thermal Design Laboratory that provide services for resolving electronics thermal issues. Mr. Kajita started system development in 2009 and recently started accepting purchase orders from customers interested in purchasing the system. Mr. Kajita says, "Measuring the amount of heat generation from electronic parts may seem easy, but it is actually quite difficult. The amount of heat generation is extremely important for thermal analyses. This is the first system that enables users to measure the amount of heat generation from electronic devices mounted on a circuit board." HeatDesigner is a critical component of the system during the planning and verification stages.
To successfully perform electronics thermal management simulation, geometry data, thermo physical properties, and the amount of heat generation must be known. The geometry data can be measured, and thermal properties, such as thermal conductivity, can be obtained from manufacturers or measured at NMIRI. On the other hand, the amount of heat generation depends on the environment around the electronic devices. As a result, it is difficult to quantify. Facing this challenge, Mr. Kajita worked with the Thermal Design Laboratory to develop a measurement system to quantify the amount of heat generated from electronic components. The system is composed of heat sinks, fans, and controllers. The fan that is in contact with the electronic part is run and the amount of heat generated is measured and displayed on the computer monitor. Mr. Kajita validated the geometry of the system and the materials used for the circuit boards during the planning and validation stages of the process. At these stages, Mr. Kajita also evaluated both air-cooled and water-cooled systems. He fully utilized HeatDesigner to compare the performance between the air-cooled and water-cooled systems because changing internal materials experimentally or modifying the test system to use water would require too much time and effort. Therefore, simulating the systems with HeatDesigner is essential for development of the measuring system.
Applying HeatDesigner to Improve Measurement Accuracy
Developing measurement systems and instrumentation is one of NMIRI's most important responsibilities. CFD tools are often used as part of the development process. One example of this is the development of the laser flash method for measuring thermal constants. This device is used to measure thermal diffusivity, specific heat capacity, and thermal conductivity of solids such as metals and ceramics. To begin the process, a target circular sample is heated by irradiating it with a pulse laser. The temperature rise on the opposite side of the irradiated surface is measured with a radiation thermometer to obtain the temperature response curve. Then the temperature response curve is used to calculate the thermal diffusivity and specific heat capacity.
These values are calculated assuming the laser light density distribution is ideal. In fact, the laser light density distribution can be uneven, and the condition of the laser light varies depending on how the light is irradiated. Furthermore, the sample may not be in an ideal condition for the calculation. As a result, the uncertainty in these factors can make the calculation difficult and introduce error.
To solve this problem, the engineers at NMIRI compared the results between the simulation and actual measurements to determine the cause of error. This also helped to improve the accuracy of the simulation. Mr. Kajita says "It is sometimes said that low simulation accuracy causes the inconsistency in results between the simulation and actual measurements. However, the experiments are not always performed under ideal conditions." According to Mr. Kajita, simulation accuracy tends to decrease as the phenomena being modeled become more complex. However, for simple phenomena, the simulation results are more reliable than the experimental results.
Fig. 3 Flow field around air-cooling fan
Growing Demands for Higher Accuracy of Analysis
The demand for increasing accuracy and the detail of the modeled electronic parts continues to grow. While part geometries can be examined using the institute's x-ray machine, the part's internal material characteristics and properties are not visible using this technique. The engineers at NMIRI realized that internal material properties, heat capacity, and thermal resistance could be estimated more accurately if trends of these parameters can be developed. This is done by first presuming the inner structure of the part. Then graphs of heat capacity and thermal resistance are developed. The engineers change the materials and compare the simulation results with the experimental results. Following this process, they are able to predict the internal material of the parts more accurately.
At one time, the engineers at NMIRI used to receive simple requests to measure the thermal conductivity of an individual part and estimate the part materials. However, today many clients want more detailed simulations and verification of the parts internal materials. Mr. Kajita says, "Most companies struggle to model parts for simulation, so we feel our support of their modeling efforts is very important."
Flexible Data Application
Over the years, NMIRI has worked with many different software products. One of the things Mr. Kajita appreciates about Software Cradle products is their flexible output methods. For example, if the analyst wants to save a full transient solution, the output data file will be very large. As a result, often only necessary data is saved. With Cradle software products, a designated section of the data can be saved. This can be an average temperature in a particular region or for a specified time. Users can consider available memory capacity and define their output accordingly.
Cradle's technical support team also provided NMIRI with assistance. The Cradle staff quickly responded to inquiries and proposed alternative approaches. Mr. Kajita says, "Cradle always responded to our requests and requirements quickly. This was a major advantage compared to other software companies."
Mr. Kajita goes on to say, "The use of simulation enables the engineers at NMIRI to do what they could not do before. They could not predict thermal issues only by tests and experiments. However, with simulation, they can freely change the material and conditions. This has resulted in significant benefit."
With the growing recognition of simulation and its use, NMIRI has used the products to discuss and support needs of their clients, who had started using simulation on their own. This has led to another benefit. NMIRI engineers have been able to focus on advanced analyses while using models that were created by their clients.
Expectations for Coupled Analyses
NMIRI has asked Cradle to provide additional support to improve the software. This includes the ability to accept legacy models that are more than two versions old into the latest version of the software. This will enable the engineers to use the latest capabilities of the software while working with older models.
Mr. Kajita also feels that multiphysics is becoming increasingly important based on his work with a number of companies. He would like Cradle to excel in this development as well. Mr. Kajita says, "Rushing development may result in unwanted functionality and software that is not easy to use. We strongly hope that Cradle will take the time to develop un-rivalling high quality multiphysics capabilities.
More Opportunities for Simulation Software
Engineers in the electronics industry face many thermal challenges as electronic devices become smaller and lighter. While simulation is ideal for addressing these challenges, Mr. Kajita feels that, despite the growing popularity of CFD tools, only a few actually use the tools. He believes that for many of his clients, their designers lack basic knowledge of fluid and heat transfer. Even though they work closely with NMIRI, they still have difficulties solving their heat transfer problems.
To help resolve this deficiency, Mr. Kajita plans to offer a series of seminars designed for those who have never used simulations tools. The emphasis of the seminars will be to familiarize the designers with how to use the tools to solve thermal problems. Mr. Kajita says, "The actual operation of CFD software can significantly help inexperienced designers understand thermal issues much more effectively than by looking at the numerical expressions." He also thinks that simulation software is not well established with respect to application, modeling method, and utilization. One of his personal objectives is to continue his studies to improve these issues.
At the same time, Mr. Kajita is always looking for collaborators who will work with him to conduct this extensive research. He believes CFD tools have plenty of room for further research. By advancing the technology, NMIRI will continue to provide valuable and dependable services to their clients.

Nagoya Municipal Industrial Research Institute
- Established: 1935
- Operation started: 1937 as Nagoya City Industrial Guidance Center
- Business: Technical support for small and medium-sized companies
- Location: Nagoya city, Aichi, Japan
*All product and service names mentioned are registered trademarks or trademarks of their respective companies.
*Contents and specifications of products are as of August 1, 2013 and subject to change without notice. We shall not be held liable for any errors in figures and pictures, or any typographical errors.
Download