Kanazawa Institute of Technology, College of Engineering

Helping Students Acquire a Basic Knowledge of CFD through the Implementation of CFD
In the Department of Aeronautics and Department of Mechanical Engineering at the College of Engineering of Kanazawa Institute of Technology, SC/Tetra, a thermo-fluid analysis software product, is used as a part of their curriculum. This general-purpose tool helps students learn the basic applications of CFD, which is essential in the aeronautics field. Associate professor Daisuke Sasaki (Picture 1) of Department of Aeronautics explains how they apply CFD in class.
Picture 1: Associate professor Daisuke Sasaki (PhD in Information Science), Kanazawa Institute of Technology, College of Engineering, Mechanics field, Department of Aeronautics
In the Department of Aeronautics and Department of Mechanical Engineering of Kanazawa Institute of Technology (KIT), general-purpose CFD tools are widely used in classes and for graduation works. SC/Tetra has been adopted by Associate professor, Daisuke Sasaki, who specializes in aerodynamic design and computational fluid dynamics. He explains how they use the software in class and shares feedback about the software from students.
One of Dr. Sasaki’s research themes is analyzing complicated geometries of airplanes and fluid machine efficiently and accurately with Cartesian mesh. His research also aims to reduce variation in the analysis results, which can be varied depending on tool (meshing) users. In fluid analyses, unstructured mesh is used in most cases as with SC/Tetra. However, when Cartesian mesh is used, users generate mesh comparatively in the same way. This way, differences in analysis results can be reduced, regardless of tool user. The process to generate mesh can also be simplified using Cartesian mesh instead of unstructured mesh. In addition, Dr. Sasaki works through robust aerodynamic optimization using CFD. The term ‘robust’ means that the performance of an object does not vary significantly even if its shape or conditions slightly differ from those at the design point. For airplanes, if the performance such as drag and lift varies significantly depending on Mach number or angle of attacks, the design is below the acceptance level. Every year in KIT, for example, students create human-powered airplanes to participate in contests where they compete in terms of flight distance and time. In the process of creating airplanes by themselves, they sometimes find geometrical differences between the original design and final outcome. To solve these kinds of issues, he proposes to achieve design approaches that can secure the product performance under a certain level of shape variety.
Introducing a Software Package
SC/Tetra was already used in KIT when Dr. Sasaki started to work there in 2012; however, they had used an earlier version for five or six years because they had a paid-up license. At that time, Windows 8 was released, and Dr. Sasaki and some of his fellow colleagues at the School of Engineering decided to update the tool.
“One of SC/Tetra’s advantages is that it is a software package”, said Dr. Sasaki. He continues: “One software package includes the preprocessor (meshing), the solver, and the postprocessor (visualization). We can easily work through a series of tasks with SC/Tetra in classes. If they were not packaged, we had to purchase each module such as a mesh generation tool separately.
Picture 2: Numerical simulation class in the Department of Aeronautics during the case study interview
Widely Experiencing CFD including Compressible Fluids in Classes
SC/Tetra is used in many courses, which include two third-year courses: ‘Numerical simulation’ in the Department of Aeronautics, and ‘Fluid Dynamics’ in the Department of Mechanical Engineering. In addition, the software is used in classes and for graduation works of the master’s courses and the undergraduate courses. In the Department of Aeronautics, students operate the CFD tool for the first time at the latter period of the third year in the ‘Numerical simulation’ course (Picture 2).
The course lasts 16 weeks. Students study structural analysis in the first 8 weeks. Then, they acquire basic knowledge about the simulation tool and learn how to use the tool using a general-purpose CFD tool in the second 8 weeks. SC/Tetra has been adopted as the CFD tool of choice for this course.
During the following 8 weeks, one topic is given every two weeks and the students write reports on each topic. The four topics given in the course are high-speed flow, unsteady flow, turbulent flow, and a topic that each student chooses and solves by himself. The first topic 'high-speed flow' involves shock wave generation in an inviscid flow and includes understanding of CFD process. They also have to explain the significance of mesh generation. In the second topic, students analyze flows around a cylinder. Then, they analyze turbulent flows around an airfoil.
Basics of CFD are explained in the first 30 minutes of the classes, and students work on the exercises in the rest of the 60 minutes. In these exercises, students generate mesh, create analysis conditions, conduct calculations, and visualize the analysis results by themselves based on the given information.
Learning the Nature of Fluid Analysis
Dr Sasaki said that the goal of the course is to understand the operation flow of the fluid analysis tool. The reason why compressible fluid with shock waves is the first topic given in the course is as follows; the software provides the simulation results even if a flow which has to be set as compressible is set as incompressible, thus, students may not recognize the mistake but may assume it is appropriate when they conduct analyses. As for mesh generation, Dr. Sasaki wants his students to acquire the basic knowledge necessary for CFD analyses, including why finer mesh is located in a specific area and what happens if mesh is extremely fine. After acquiring the basic knowledge sufficiently, they should study what they need.
Picture 3: Mr. Yuki Imura (left side) and Mr. Kensuke Nishii (right side) in the third year of the Department of Aeronautics
At the time of the interview, it was the end of the first week for fluid analysis in the numerical simulation course. We asked the students how SC/Tetra was, and they gave us the same feedback that the software was easy and user-friendly in generating mesh. “In the structural analysis we worked on previously, we had to input numbers to specify the range. With SC/Tetra, the range can be specified on the model. It was much easier (Mr. Yuki Imura in the third year of the Department of Aeronautics/left side in Picture 3).” On the other hand, another student comments: “We have a hard time adjusting to CFD terminologies (Mr. Kensuke Nishii in the third year of the Department of Aeronautics/right side in Picture 3).”
Dr. Sasaki says it seems difficult for students to operate the tool appropriately for the first time. SC/Tetra has more setting items than a typical structural analysis tool. They have to adjust themselves to the tool and tend to make mistakes in setting boundary conditions. Sometimes they specify wrong conditions for all six surfaces. A calculation may stop on the way, or the analysis result may not be correct. Once they succeed, they will improve their skill by themselves.
Picture 4: Ms. Saori Tanji in the third year of the Department of Aeronautics
Ms. Saori Tanji (Picture 4) in the same course worked as an intern for a design company last year. She learned how to use SC/Tetra throughout the day and operated it with an in-house manual. She said “I understood what I had done reviewing it the next day.” From her comment, we see that students have a hard time adjusting themselves to CFD tool operation; however, they will understand the tool operation flow and achieve positive results by experiencing a series of the tool operation procedure.
Analyzing an Arbitrary Geometry such as a Human-powered Airplane
For the fourth topic in the course, the students use a provided airfoil model or other customized model of what they want to analyze, calculate the model, and write a report. To set material properties and the information on the flow, they have to research and decide the parameters by themselves. Last year, about the half of the students analyzed what interested them. For example, one student added his unique parts to the existing airfoil and compared the performances, and another student analyzed the motion of a hockey puck.
Picture 5: Mr. Kota Nishioka in the third year of the Department of Aeronautics
In KIT, for craftsmanship-related extracurricular activities, students can join the human-powered airplane project and the small unmanned aerial vehicle project. Many students who enroll in the course are also in the project, and some of them want to analyze the flow of the airfoil they are using. Mr. Kota Nishioka (Picture 5) took the course piloted a human-powered airplane last year and designs the airframe this year. He has been using SC/Tetra since last year for design and simulates how much drag of the airplane can be reduced. He also says he wants to calculate the air flow inside the cockpit fairing. If the air intake position is not appropriate, the inside cannot be cooled and will be extremely hot.
Picture 6: Teaching assistants - Mr. Taiki Kunishio (left side) and Mr. Takuya Hirose (right side)
Manuals Help Beginners Understand SC/Tetra Operation
We also interviewed two teaching assistants. Mr. Takuya Hirose (right side in Picture 6) is in the second year of the master’s course in mechanical engineering. He used SC/Tetra for the first time when he was in the laboratory. He had a hard time in his early period to analyze a valve with two inlets and one outlet, because various parts were assembled, he had to remove the interfered surfaces. Now he uses SC/Tetra to verify an in-house program using Cartesian mesh for analyzing the flow inside a combustion chamber of a solid rocket. He mentioned the calculation stability as one of SC/Tetra’s advantages.
Mr. Taiki Kunishio (left side in Picture 6) in the first year of the master’s course has used SC/Tetra since he operated it for the first time in class. At first, error messages used to appear even though he followed the operation procedure, and he could not find the causes. Now however, he can predict the error causes, e.g., mesh and boundary conditions. In addition, he can solve most of his problems by referring to the manual provided by Software Cradle. He says “The manuals are written for those who work on CFD for the first time, and basic terminologies are explained. Therefore, even beginners can understand CFD and the software operations broadly.
Figure 1: Analysis of unsteady laminar flow around a cylinder to understand a unsteady flow field
Dr. Sasaki says that students should refer to the manual provided by Software Cradle to improve their application skill. The manual contains exercises using models similar to their analysis targets. In addition, the second topic 'unsteady flow around a cylinder' (Figure 1) can be compared with a wind tunnel experiment of a flow around a cylinder conducted in the third year course. By using these tools, students are expected to enrich their understanding for CFD.
Increasing Demands for CFD
Fluid analyses are used not only in fields tightly connected to fluids, such as aircrafts and fluid machinery, but also in other fields. Because many of the fields which mainly conduct engineering experiments are related to fluid, analysis tools are expected to be helpful also in those fields. For example, there is a group in KIT who study Japanese swords involving their functional beauty and structural materials. In the multidirectional approaches of the study, students conduct wind tunnel experiments and analyze aerodynamic noise using a CFD tool. On the other hand, demands for CFD among companies are increasing. Many small- and medium-sized companies have difficulty introducing fluid analyses despite their interests. From this point, CFD education for students is extremely beneficial.
Dr. Sasaki has a prospect to apply his studies to moving objects and rotating objects using SC/Tetra. Recently, demands for CFD have been increasing especially in drone fields. They expect to use CFD to improve the aerodynamic performance of drones for more safety and longer battery life. Dr. Sasaki hopes to work with these organizations and provide advice from aerodynamic perspective aspects.
In addition, he continues to study robust design and effective optimization methods with appropriate design conditions and fewer calculations. The optimization program (design tool) Dr. Sasaki developed can be used in combination with commercial tools such as SC/Tetra.
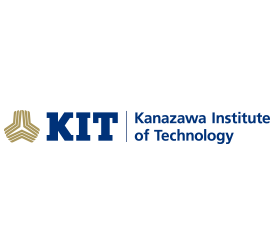
Kanazawa Institute of Technology
College of Engineering
- Founded: April 1, 1965
- College: Established in 1965
- Location: Nonoichi-shi, Ishikawa
- Type of university: Private
*All product and service names mentioned are registered trademarks or trademarks of their respective companies.
*Contents and specifications of products are as of November 30, 2016 and subject to change without notice. We shall not be held liable for any errors in figures and pictures, or any typographical errors.
Download