South Dakota School of Mines and Technology
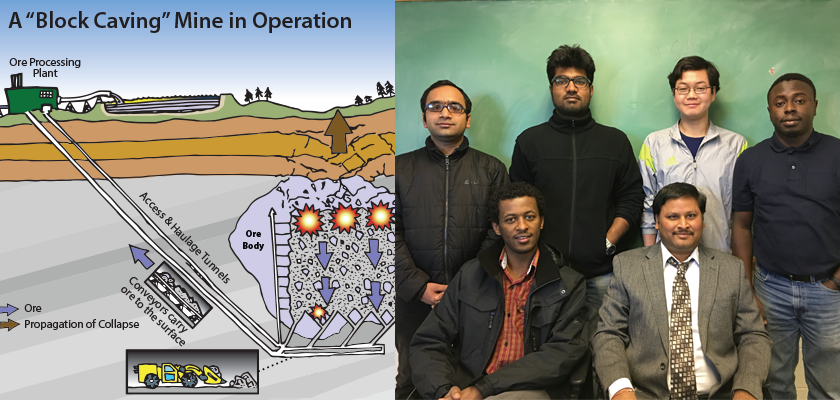
Students Use Simulation Technology to Improve Underground Mine Safety
Historically, improper mine ventilation has caused major disruptions in mining operations and can endanger worker health and safety. This paper discusses research being performed by students at the South Dakota School of Mines and Technology to better understand ventilation in mines. The students used Software Cradle’s SC/Tetra CFD software to simulate the airflow inside the working areas of the mine. The following narrative interview highlights their achievements.
Using CFD to Better Understand Underground Mine Ventilation
Picture 1: (left to right, standing) Rahul Bhargava, Saiprasad Sreekumar Ajitha, Yong Pan, Kayode Ajayi
(left to right, sitting) Gemechu Turi, Dr. Purushotham Tukkaraja.
The ventilation of an underground mine presents a significant challenge for mine engineers who must ensure the work environment in the mine is properly ventilated. Air flow and pressure throughout a mine cannot be seen. In addition, conducting physical tests inside the mine is usually not feasible in the majority of cases.
Traditionally, mine engineers have had to rely on one-dimensional empirical formulas and their experience to design ventilation systems for underground mines. The fluid dynamics in a mine is extremely complex and does not always lend itself to being modeled accurately in this way. The advent of three-dimensional simulation tools and high powered computing platforms have elevated CFD modeling to become an important area of research for mine engineering universities. Consistent with this, the Mine Ventilation Research Group at the South Dakota School of Mines and Technology found that CFD simulation can be an accurate method for assessing ventilation conditions in mines.
The group at the university is led by Dr. Purushotham Tukkaraja. The work has been funded through a research grant from the National Institute for Occupational Safety and Health (NIOSH) and has resulted in two published papers about using CFD to simulate block/panel cave mining ventilation. Two additional papers have been accepted for publication in the proceedings for the 16th North American Mine Ventilation Symposium.
“CFD has been a very useful tool for this group because simulating the ventilation of an underground block/panel cave mine, as it develops, is quite complicated. The porous media model, diffusion model, and chemical reaction model have been at the core of the group’s research.” - Dr. Purushotham Tukkaraja
Using CFD is a practical way for mining engineers to visualize and accurately determine mass flow rates, pressure losses, and gas diffusion throughout a mine.
Block Cave Mining
Block cave mining is an underground mining technique that is more cost effective and productive than traditional open pit mining methods. This technique involves cutting two sets of tunnels, one directly on top of the other, underneath the orebody, which is located deep within the earth. The lower level tunnels are used as the extraction site (also called the production level). The upper level tunnels (undercut level) are used as a drilling site where explosives are detonated to break up the rock and initiate caving. Once the explosives are detonated, the rock fractures into smaller pieces. Vertical drilling at the draw points help encourage the broken rock to begin to crumble and fall. The material can then be continuously removed. As the ore is removed, gravity causes more rock to fracture, break up, and fall into the draw points. When this process is performed properly, the rock will continuously cave under its own weight, producing a continuous flow of ore to the draw points.
Figure 1: A “Block Caving” Mine in Operation
Figure 2: 2D Block Cave Model
As the rock caves, an air gap grows between the broken rock region and the zone above where the rock has not yet caved. Using special equipment, miners continually monitor the air gap because if it becomes too large it could collapse violently. This could cause an air blast which could kill or injure workers. By using the monitoring device to assess the rate of caving versus the rate of production, mine engineers can maintain control of the air gap size. From a ventilation stand point, Dr. Tukkaraja’s group used CFD to determine an optimal air gap height to achieve adequate ventilation in the mine.
Another unseen hazard to the miners, in the case of extraction orebody with uranium mineralization, is the release of hazardous radon gas into the working environment. Radon is a tasteless, odorless, inert, radioactive, and likely carcinogenic gas. As the rock is broken, radon gas is released into the mine. To ensure the working environment is safe, the radon concentration in the working area must be diluted to a safe level. For block cave mining, engineers currently use empirical relationships to determine how much fresh air they need to supply to dilute radon concentrations to a safe working level. However, these relationships do not help engineers to know the actual radon concertation at different locations in the mine. Furthermore, studies have shown that these empirical relationships fail to estimate the amount of air that is required to dilute radon gas to a safe level.
CFD Analysis of Block Cave Mining
The Mine Ventilation Research Group at the South Dakota School of Mines and Technology used Cradle’s SC/Tetra CFD software to better understand how the air gap affects the ventilation system in block caving mines. The students modeled different cave geometries having different air gap heights. The students then conducted a steady state CFD analysis on each of the models using the same inflow velocity condition for each of the air gaps. By using a velocity condition, the mass flow through each geometry will be the same; however, the pressure difference between the inlet and the outlet will vary.
Figure 3: Image showing velocity contours of CFD domains used to represent different air gap heights
CFD Model used to Represent the Block Cave
The students tracked the pressure drop across the cave from the intake to the exhaust side for each of the air gap heights. Knowing the mass flow and the pressure drop, the students calculated the cave resistance and shock loss. Cave resistance and shock loss values help engineers define the resultant pressure loss of a cave system and the mass flow rate and enable engineers to select fans and configurations that keep the mass flow moving through the mine.The students observed that for air gaps from 4 m to 12 m, the cave resistance and shock loss across the mine initially decreased. Then it reached a minimum as the air gap grew from 12 m to 18 m. Finally, cave resistance and shock loss started to increase as the air gap height grew over 18 m.
Radon Concentration Prediction
The next step in the research was to use CFD to simulate radon gas distribution throughout the mine. Experimentally, mining engineers cannot monitor radon concentration at every location inside the mine. As a result, Using experimental data to predict radon levels throughout the mining network is virtually impossible. CFD offered a viable alternative.
Radon is characterized as a radioactive gas, meaning it constantly releases radiation. As the radon gas decomposes (decays) into more stable (less radioactive) elements, radiation energy is released. These elements are called radon daughters. The rate of the decay is called the half-life, which is the time for one half of the radon mass to decay into its daughter element. Some of the elements in the radioactive decay chain have short half-lives and some have longer half-lives. Due to this decaying process, the gas density actually changes with time. The students used the SC/Tetra’s chemical reaction function to model the radon decay process. This enabled the simulation to account for the changing properties of the decaying radioactive gas as it is dispersed throughout the mine.
Upon the completion of the simulation, the students needed a way to verify their model accuracy. To do this, they compared their results to the generally accepted empirical relationship between the quantity of fresh air supplied and the amount of radon concentration diluted. The results were in agreement and the discrepancy is thought to be due to the assumptions made in the empirical model. Furthermore, past research suggests that the empirical model underestimates the amount of fresh air needed and is in agreement with the students’ findings.
The method the students used to model the radon gas needs to be further validated; however, the preliminary results are good and show a number of promising advantages over empirical methods. The empirical prediction only accounts for the radon level at the exit of the airway, whereas CFD allows engineers to account for spatial and time dependent radon mitigation. Therefore, using CFD, engineers will be able to predict the actual concentration of the radon throughout the mine. This is in addition to being able to most likely make much better predictions about the amount of supplied fresh air needed to dilute radon concentrations to a safe level.
Industry and academia will need to collaborate to validate the CFD models with field/experimental data. Dr. Tukkaraja offered some insight about the acceptance of CFD simulation in the mining industry.
“CFD has been slow to gain popularity among mining engineers because the verification of the results is hard to obtain. This is because field studies and experimental results are required for verification of CFD results. In some mining applications, it may not be feasible to verify the CFD results for some cases. However, as more results from CFD are validated, more and more of the people in the mining industry will see a reason to explore CFD as a research and development tool.”
Cradle SC/Tetra and Mine Ventilation Simulation
The Mine Ventilation Research Group at the South Dakota School of Mines and Technology chose Cradle’s SC/Tetra CFD software because of its robust and easy to use pre-processor which was useful in modeling the complex block cave mining domains. SC/Tetra was also chosen because of the software’s ability to model many different physical phenomena, including chemical reactions. However, one of the most important reasons SC/Tetra was chosen was because of the excellent, fast, and friendly technical support that Cradle North America provides.
Dr. Tukkaraja summarized these challenges saying:
"One of the most challenging aspects of CFD application in the mining industry is the complexity of mining operations. Most of the underground openings include a number of tunnels with different designs which makes it hard to fully represent in the software. The complex geometry of mining operations also introduces meshing problems in CFD simulations.”
He also offered comments about the value of working with Cradle and using SC/Tetra for mine simulation.
“In general, SC/Tetra is a great tool to use for underground mine ventilation applications because the software is user friendly and can efficiently solve the large meshes that will be used to model the underground mining domains. We continue to use Cradle because of the excellent technical support that they have been providing to us.”
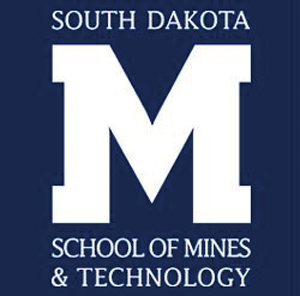
South Dakota School of Mines and Technology
- Founded: 1885
- Accreditation: The Higher Learning Commission
- Location: Rapid City, SD, USA
*All product and service names mentioned are registered trademarks or trademarks of their respective companies.
*Contents and specifications of products are as of March 31, 2016 and subject to change without notice. We shall not be held liable for any errors in figures and pictures, or any typographical errors.
Download