Basic Course on Turbulence and Turbulent Flow Modeling 6: 6.1 Properties of turbulent flow phenomena and difficulties in their calculation, 6.2 Turbulence model and coarse graining
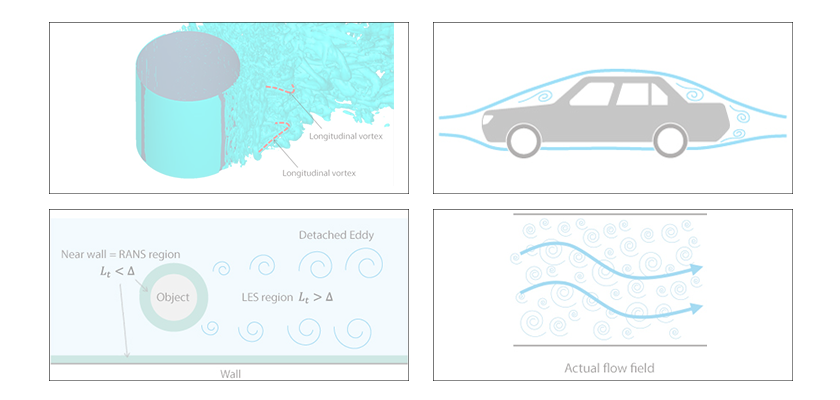
Why is turbulent flow calculation difficult?
6.1 Properties of turbulent flow phenomena and difficulties in their calculation
It is generally said that a fluid analysis is difficult; especially a turbulent flow calculation is the most difficult. Why is a turbulent flow calculation so difficult? Are the fluid equations complex? Or, does “fluid analysis is difficult” mean “solving the equations is difficult”? Of course, neither of them is easy; however, there is another big reason. It comes from characteristics of a turbulent phenomenon. In the column No.3 and No.4, it is described that a turbulent flow (vortex tube) is generated by velocity difference, the generated tube induces another vortex tube, and vortex tubes are generated one after another in the same manner. In the columns, it is also said that a newly generated vortex tube is smaller than the original one. This is the important point. “A newly generated vortex tube is smaller than the original one” means that the size of phenomenon (vortex tube) to be captured becomes small endlessly due to the characteristics of a turbulent flow, which makes a turbulence calculation difficult. Why is this a problem? This is a problem because infinite calculation mesh is required to simulate endlessly generated smaller vortex tubes. Actually, Kolmogorov length is the minimum size of vortex tubes. Even so, preparing mesh to capture all vortex tubes is practically impossible.
6.2 Turbulence model and coarse graining
It is impossible to prepare calculation mesh for unlimitedly generated smaller vortex tubes. Therefore, a way to simulate a turbulent flow is required. The way is “turbulence model”. The effect of vortex tubes that are too small to be captured with mesh can be taken in simulation by using the turbulence model. Then, the required mesh size is limited and a realistic calculation can be done. The treatment is called “coarse graining”. (Figure 6.1)
Figure 6.1: Coarse graining of vortex tubes
The coarse graining is not specific for a turbulent flow calculation and is used to establish fluid basic equations. The equations are so-called Navier–Stokes equations. In the equations, there is a part which describes the effect of fluid viscosity. The viscosity is the result of coarse graining of the motion of a fluid. Let us see the viscosity in detail.
The minimum unit of fluid motion is at the molecular level. To calculate the motion by using finitely generated calculation mesh, the motion must be represented by mesh whose size is greater than a molecule. Therefore, the motion of a fluid is expressed by a mass of molecules. The motion of each molecule such as intermolecular force and thermal motion of a molecule is not considered; however, the interaction between masses of molecules is expressed by equations. This is the model that expresses “viscosity is proportional to velocity difference”. You can actually “feel” this model when you move a board on water by your hand. When you move the board slowly, you need a small force. When you move the board fast, you need a large force (Figure 6.2). You can apply this viscosity model to most flow fields. In other words, this model is a universal model.
Figure 6.2: Viscosity model
For turbulence models, some models have been suggested with the same way of thinking as viscosity in which velocity difference is multiplied by a viscosity coefficient. Other various turbulence models have also been suggested; however, a universal model like the viscosity model has not been suggested as of now. Therefore, turbulence models are used depending on calculation problems. Vortex tubes that become endlessly smaller as mentioned above and the fact that no turbulence model is universal are making the calculations of turbulence difficult. If a universal turbulence model is suggested, a turbulent flow calculation will be solved with less difficulty.
About the Author
Takao Itami | Born in July 1973, Kanagawa, Japan
The author had conducted researches on numerical analyses of turbulence in college. After working as a design engineer for a railway rolling stock manufacturer, he took the doctor of engineering degree from Tokyo Institute of Technology (Graduate School of Science and Engineering) through researching compressible turbulent flow and Large-Eddy Simulation. He works as a consulting engineer at Software Cradle solving various customer problems with his extensive experience.