Master Course for Fluid Simulation Analysis of Multi-phase Flows by Oka-san: 1. Introduction

Introduction
Yutaka Tsuji is professor emeritus in the school of Mechanical Engineering at Osaka University and is an expert in the analysis of multi-phase flows. I was first exposed to multi-phase flow analysis at one of Professor Tsuji's seminars. His seminar was full of humor which made the topic interesting to me. Multi-phase flow analysis ultimately became the focus of my studies largely due to the impact that Professor Tsuji's lecture had on me. A few years later, Grade 1 for analysis engineers in thermal fluid mechanics was added to the certification program for computational mechanics engineers sponsored by the Japan Society of Mechanical Engineers. I worked to learn the analysis skills, and passed Grade 1 for multi-phase flow analysis. And now, I am writing this column about multi-phase flow analysis.
What is multi-phase flow analysis? It is a scientific term. One way to develop an understanding of the phrase is to look at the words individually. The word “phase” in “multi-phase flow analysis” stands for the three different possible states of an object, namely the gas, liquid, or solid phases. “Multi-phase” means two or more phases are present and can be classified into four types: gas-liquid two-phase, gas-solid two-phase, solid-liquid two-phase, and gas-liquid-solid three-phase. In addition, two immiscible liquids such as water and oil are called liquid-liquid two-phase and may also be included in a multi-phase flow analysis. (See Figure 1.)
Figure 1: Classification of multi-phases
A multi-phase flow analysis simulates a multiphase flow. The analysis method is computational fluid dynamics (CFD). The phrase “fluid simulation analysis” may also be used.
Example of multi-phase flow analysis
Here are some analysis examples to provide a better understanding about what a multi-phase flow analysis is. The milk crown phenomenon is a typical example of a gas-liquid two-phase flow (Figure 2). A crown shape is formed when a liquid droplet impinges against a thin liquid film. The shape of the crown is most easily captured by high-speed photography. In Figure 2, the free surface flow that is the interface between air (gas phase) and liquid (liquid phase) is analyzed.
Figure 2: Milk crown phenomenon
A cyclone separator is a good example of a gas-solid two-phase flow. The separator literally separates air and powder using the centrifugal force. This is the mechanism used in a cyclone vacuum cleaner. In Figure 3, the flow of air (gas phase) is analyzed along with the flow of the powder (solid phase) using the particle tracking method.
Figure 3: Cyclone separator
Ice-making system is a typical example of a liquid-solid two-phase flow. In Figure 4, the transparent region represents water, and white region represents ice. In this analysis, the phase change between ice (solid-phase) and water (liquid-phase) is modeled, i.e., solidification and melting.
Figure 4: Ice making
A rising oil droplet in water is an example of a liquid-liquid two-phase flow. The analysis approach depends on the number of oil droplets. In Figure 5, the free surface flow that comprises the interface between two liquid-phases is analyzed and the surface tension force is considered.
Figure 5: Oil droplet
Solidification of molten metal is an example of a gas-liquid-solid three-phase flow. Air (gas phase), molten metal (liquid phase, red region in the figure), and a solidified metal (solid phase, gray region in the figure) coexist. In Figure 6, a free surface flow and a solidification/melting model are used together to analyze the phenomenon.
Figure 6: Solidification of molten metal
These examples provide a glimpse of the kinds of multi-phase flows that can be simulated using computational analysis. However, many multi-phase flow phenomena are very complex, so not all multi-phase flows can be analyzed computationally. Even so, continued improvements in computer hardware and software capabilities are making multi-phase flow problems solvable using fluid simulation analyses.
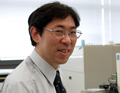
About the Author
Katsutaka Okamori | Born in October 1966, Tokyo, Japan
He attained a master’s degree in Applied Chemistry from Keio University. As a certified Grade 1 engineer (JSME certification) specializing in multi-phase flow evaluation, Okamori contributed to CFD program development while at Nippon Sanso (currently TAIYO NIPPON SANSO CORPORATION). He also has experience providing technical sales support for commercial software, and technical CFD support for product design and development groups at major manufacturing firms. Okamori now works as a sales engineer at Software Cradle.