Tokai University
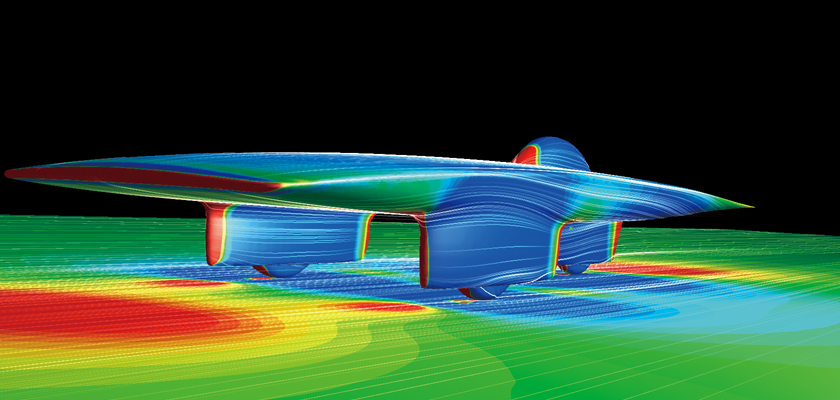
Students Take the Lead in Simulating Solar Car Aerodynamics
The Solar Car Team at the Tokai University Student Project Center (Kanagawa, Japan) has to be considered one of the premier student-led solar car design teams in the world after winning back to back World Solar Challenge races (2009 and 2011) in Australia. A critical aspect of successful vehicle design is minimizing aerodynamical drag since one major goal is to achieve high speeds while using minimal energy. The Tokai student-led team used Computational Fluid Dynamics (CFD) simulations to optimize the vehicle geometry. In particular they used Software Cradle SC/Tetra CFD Software for the simulations. Following are highlights from an interview with the Tokai team that discussed the educational advantages and usability of SC/Tetra in this challenging environment.
About the Tokai University Student Project Center
The Solar Car Team belongs to the Light Power Project at the Tokai University Student Project Center. The Center is an educational organization that provides a nucleus for student-led activities following various themes. These themes range from local revitalization to environmental issues and social actions. Activities include participation in competitions, joint projects with industry, and hosting workshops. Using these activities, the Center helps students learn fundamental skills that will help them in their professional careers and in life. These include communication, leadership, problem-solving, and inventiveness. In addition to the Solar Car Team, other teams include the Electric Vehicle Team, and the Human-Powered Aircraft (HPA) Team. These three teams are a part of the Light Power Project, which is focused on designing environmentally friendly means of transportation.
Dr. Hideki Kimura, Professor, Department of Electrical and Electronic Engineering, School of Engineering, Tokai University,
Assistant Executive Director, Tokai University Student Project Center
The first Solar Car Team was assembled in 1991. The Tokai University Student Project Center was established in 1996. The team works within the Prof. Hideki Kimura Laboratory under the Department of Electrical and Electronic Engineering. Dr. Kimura is the Assistant Executive Director of the Student Project Center. Students from various schools within the University are Solar Car team members. These include participants in Engineering but also students from the Department of Arts.
About the Tokai Challenger
Solar cars are the ultimate environmentally friendly vehicles. They run solely on solar energy and batteries. Once on the road, they do not require any refueling. The Tokai Challenger, the solar car created by Tokai University, uses the most advanced technologies in the industry. It uses optimized Panasonic silicon series HIT Solar Cells, which have a 22% conversion efficiency with 5KWh lithium-ion batteries. The vehicle's frame is constructed from CFRP (carbon fiber reinforced plastic) manufactured by DOME Carbon Magic Co., Ltd., and carbon fibers are supplied by Toray Industries, Inc. The high efficiency motor is produced by Mitsuba Corporation. The car is 4.98 m (16.3 ft) long, 1.59 m (5.2 ft.) wide, and .88 m (2.9 ft) high. It cruises at 90 km/h (56 mph) using solar power and has a theoretical maximum speed of 160 km/h (99 mph).
Tokai University Student Project Center
The Tokai Challenger won the Australian World Solar Challenge in 2009 and again in 2011. These are back to back wins since the race takes place every other year. In addition, the team won three straight "Solar Challenge South Africa" races in the Republic of South Africa from 2010 to 2012.
Using SC/Tetra for Solar Vehicle Design
The design of the solar car begins with a three dimensional body design, in accordance with competition regulations, using SolidWorks CAD software. The 3D geometry data is input into SC/Tetra CFD software, which is used to run aerodynamic simulations to optimize the vehicle geometry. SC/Tetra has been used for the aerodynamic simulations at Tokai University since 2009. At that time the simulations were performed with the help of Atsuya Ikegami and Kiyoshi Shimada, experts in body design and aerodynamics at Yamaha Motor Co., Ltd. During those early days, determining the vehicle geometry was largely a trial and error process. They first began by simulating the designs of their competitors. From there they sought to incrementally reduce air resistance by minimizing CDA (the product of aerodynamic drag and projected area).
Dr. Kota Fukuda, Department of Aeronautics and Astronautics, School of Engineering, Tokai University
Students are a central part of the design and simulation process and lead the detailed engineering and analysis work. They work under the guidance of Dr. Kota Fukuda, the aerodynamics expert and lecturer at the Department of Aeronautics and Astronautics. Dr. Fukuda began guiding the simulation work when he came to the University. Currently three students are skilled at performing the vehicle aerodynamics simulations.
Simulating a Variety of Geometries
Unlike the early days, when the team started their designs by analyzing competitors' designs, the mindset today, as described by Dr. Kimura, is, "We don't show any specific examples. We let the students design freely". This enables the students to be unconstrained by the past and to think out of the box. This approach can lead to unanticipated and novel designs.
Students performing simulations on their own
When designing a solar car, the first physical limitation is the large surface area needed for mounting the solar cells. Aerodynamic efficiency is a critical performance criterion. In addition, the cockpit size and overall vehicle dimensions must be within the competition regulations. 3D CAD data is passed to SC/Tetra by converting IGES format into STL. In the early days, this data conversion was difficult. Because of moving parts, such as the axles, the wrapping function could not capture all the geometry modifications. Over time, the expertise to perform the data conversion has been developed, reducing the time needed to perform this task. In addition, as the vehicle matures, fewer vehicle geometry modifications are required. Today, a single CFD simulation can be performed in approximately eight hours using a vehicle half model.
Because of the constant change of students at the University, the Solar Car Team realized the importance of training. Not only do students attend lectures given by Yamaha Motor and Software Cradle staff, they also teach each other and instruct their junior colleagues.
Why SC/Tetra is so Good
According to Dr. Fukuda, the advantages of SC/Tetra are its ease of operation and high accuracy. "The most important part in fluid dynamics simulation is to generate the mesh accurately". This is accomplished quite easily using the automatic mesh generation capabilities in SC/Tetra. It reduces the stress of mesh generation and facilitates evaluation of more geometry variations.
About accuracy, Dr. Kimura said, "It [SC/Tetra] never goes wide of the mark. When we modify part of the geometry, it shows up in the result. With some other simulation tools, it often happens that when we tweak some parameters, the result comes out the opposite of the facts we know. SC/Tetra simulates this sort of relative changes correctly; we can trust it."
Usability from an Educational Perspective
As a whole, SC/Tetra is well received by the students. They can clearly see how design changes affect the air flow around the vehicle. Visualizing the impact of their design changes creates excitement.
Tokai Challenger
Dr. Fukuda also emphasizes the educational advantages of SC/Tetra software. "Simulations can be performed in a relatively short time frame using SC/Tetra. This makes it suitable for classroom use". The software is appreciated not only by engineering students but also by industrial design students. More and more, industrial designers are expected to pay attention to the functional aspects of products and not just the aesthetics. For example, in automotive design, a design that is visually attractive but has low aerodynamic performance may not be accepted. Dr. Kimura says, "There are some students who want to pursue their careers in car design. For them, the process of designing and getting feedback from functional computational simulations presents an opportunity to get the feel of their future work".
Continuing on the Winning Track
The Solar Car Team is now in the middle of the design process for their entry in World Solar Challenge 2013 where they aim for their third consecutive win. Competition regulations have changed drastically since the last competition, requiring major modifications to the car body. The regulation changes are aimed at increasing safety and practicality. For example, the new vehicle configuration is a four wheel vehicle instead of a tricycle. The driving position must now be similar to that used in a conventional passenger car. The overall size of the vehicle is smaller. In sum, these new requirements suggest inferior aerodynamic performance compared to past solar cars. Consequently, the contributions from computational simulations become even more critical.
The Australian World Solar Challenge has been held since 1987 and is the most highly regarded solar race. In 2011 thirty seven teams from twenty nations and territories participated. The contesting cars run approximately 3000 km (1864 miles) across the country with 700 km (435 miles) being on highways. This amounts to about five days on the highways. When the Tokai Challenger won in 2011, it completed the route in 32 hours and 45 minutes averaging just over 90 km/h (56 mph).
In contrast, Solar Challenge South Africa is a FIA (International Automobile Federation) certified race, which is open to a variety of alternative fueled vehicles including, solar, electric and hybrid electric powered cars. While the South Africa race has fewer participants, it is much more difficult. It is the longest race covering nearly 5000 km (3107 miles) with altitudes as high as 2000 m (6562 ft). This race includes tight turns, traffic lights, and a lot of traffic on the open roads. In 2012 the Tokai vehicle completed the route in 71 hours and 13 minutes over a five day period.
Successfully competing in either solar race requires an accomplished support team. Voltages and temperatures of the solar cells are monitored at all times. This data is sent to the command and control car via radio waves by a student-developed telemetry system. Weather information is obtained from the geostationary satellite "Himawari" and converted into information the team can use for the race. Solar radiation intensities are acquired from satellite data using "T-SEED", a system developed by the Center for Environmental Remote Sensing at Chiba University and the Tokai University Research & Information Center.
Solar car races require design, development, and implementation of a broad range of technologies. The entire technical team must be fully engaged. These races challenge the comprehensive strength of the participants. From an educational viewpoint, the students develop technical skills, learn to work as a team, and often take leadership roles. This is most apparent during the aerodynamic simulation stage of the initial design, the first step toward improving the driving speed. Currently, simulations are under way for the next Challenge in Australia. The world anxiously awaits the next entry from the Tokai University Solar Car Team.
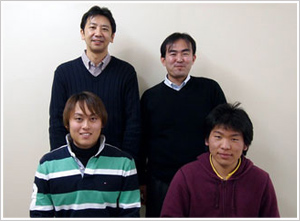
- History
- 1991: Solar Car Project launched at Tokai University
- 1996: Hideki Kimura Laboratory begins design of a high performance solar car as a member of the solar car team
- 2006: Program restructured to become the Light Power Project's Solar Car Team at the Tokai University Student Project Center
- Manager/Advisor: Professor Dr. Hideki Kimura (Top left in picture) Department of Electrical and Electronic Engineering, School of Engineering Advisor
- Lecturer: Kota Fukuda, Dr. Eng. (Top right in picture) Department of Aeronautics and Astronautics, School of Engineering
- Staffs: Ryuji Otsuka (Bottom left in picture) Sophomore in Department of Prime Mover Engineering, School of Engineering
*All product and service names mentioned are registered trademarks or trademarks of their respective companies.
*Contents and specifications of products are as of December 1, 2012 and subject to change without notice. We shall not be held liable for any errors in figures and pictures, or any typographical errors.
Download