FLUID TECHNO Co., Ltd.
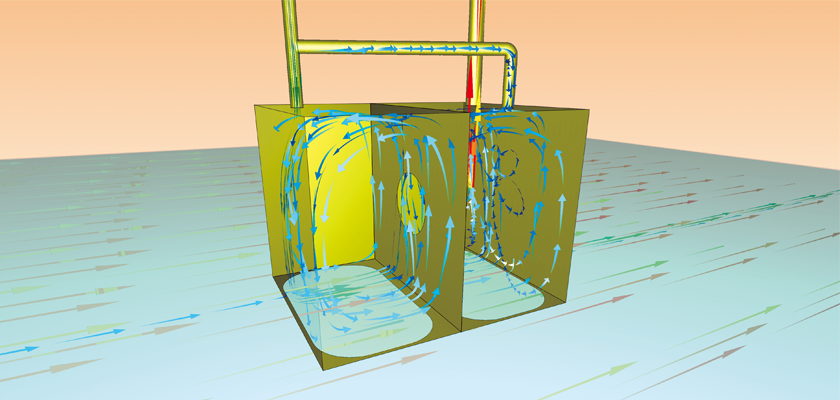
Enhancing Ship Design through Combinational Use of CFD (Computational Fluid Dynamics) and Extensive Data
Fluid Techno has cultivated advanced technologies for designing ships, providing ship-related manufacturing and training services, and developing ship-specific energy saving devices. Faced with the need to improve energy efficiency, they use Software Cradle SC/Tetra CFD software to develop more capable products in a shorter period of time.
Picture 1: Mr. Masahiro Tamashima(Dr.Eng.), President
From Hull Design to Ship Development Support Programs
Fluid Techno was founded in 2001 in Sasebo-shi, Nagasaki (Japan) and is a provider of ship design services and development support. Mr. Masahiro Tamashima, the President (Picture 1) had acquired extensive experience in ship design and experiments prior to establishing the company. Drawing upon Mr. Tamashima’s background and experience, Fluid Techno has their strengths in experience and accumulation of extensive data.
One of their business activities is ship design. Shipbuilders and ship owners contract Fluid Techno to design the hulls for a variety of ships. These range from large ships, such as very large crude carriers (VLCCs), to small and mid-size ships. Fluid Techno specializes in conceptual and preliminary designs; If likened to home design, Fluid Techno would be involved with general, up-front decisions such as whether the home will be a condominium or detached house, what shape the roof should be, and how the rooms should be laid out. This contrasts with detailed design, which, for the home example, involves determination of details such as wiring and interior decorating.
Figure 1: Eco-Stator, an energy saving stator (on left)
Reduces fuel use by 3 – 4 % for small to mid-size ships and 2 – 3 % for large ships. It has been implemented in several applications Flow in cross-sections of stern (on right) Implementation angle of Eco-Stator is determined by condition of vortices.
Fluid Techno also developed Eco-Stator, a patented marine energy saving device (Figure 1), and provided implementation services of the device when fuel efficiency goals cannot be achieved just by the original hull geometry. Eco-Stator can be installed in front of the ship propeller to improve propulsive performance by 3 - 4 % for small to mid-size ships and 2- 3 % for large ships. Eco-Stator has been implemented on more than 250 ships.
Another Fluid Techno capability is model ship design for experiments. To meet navigational requirements, experiments must be conducted using ship models. Fluid Techno offers not only special skills necessary to properly install measurement instruments inside the ship models, but also design related software programs and software for data calculations during experiments. For example, when cargo is moved by a crane from a barge (a flat bottomed boat without engines that carry heavy cargo in port or river) to a wharf, the barge position will waver due to the water motion. One Fluid Techno program calculates the acceleration at specific locations to take account for this effect. Fluid Techno also develops pre-/post-processors for fluid solvers developed by universities and research institutes.
Demand for Improved Energy Efficiency as a Driving Factor
It was the increasing demand for improving fuel efficiency that necessitated Fluid Techno to introduce SC/Tetra CFD simulation software. Most ships are designed to carry as much cargo as possible with minimum fuel usage. “As it has always been, keeping the fuel usage at minimum is the endless challenge for design engineers,” says Mr. Tamashima.
Picture 2: Mr. Takeaki Tamada, Technical Chief Manager
The demand for improved energy efficiency has gained prominence because of environmental concerns in addition to economics. Three tons of carbon dioxide is generated for each ton of fuel burned. To drive improvements, in 2013, the International Maritime Organization (IMO) began to impose regulations based on the Energy Efficiency Design Index (EEDI). Targeting ocean-going ships (come and go between nations) that exceed 400 tons, the regulation is applied to the amount of carbon dioxide generated per mile per ton of cargo. “Most of the ships we work with are subject to this regulation. I think that environmental measures will be imposed on domestic ships in the future,” says Mr. Takeaki Tamada, Technical Chief Manager at Fluid Techno (Picture 2). While regulations impose greater demands on design development, Fluid Techno sees this trend as an opportunity. “The design of the underwater section of hull is critical for improving ship performance. Our experience and knowledge will be of great use in such situations,” says Mr. Tamashima.
Figure 2: Experiment using model ship
Facilitated to measure force acting on rudder using propeller and rudder only
To obtain EEDI certification, experiments must be conducted using a model ship (Figure 2) at one of seven test facilities in Japan. Besides, the experiments are in a large scale and very costly. “CFD tool is indispensable for firms without experiment facilities like us,” says Mr. Tamada.
CFD as an Essential Tool
The ship design process starts by determining a conceptual hull shape based on the specifications given by the order. Specifications include cargo weight, velocity of the ship, and the amount of carbon dioxide in the exhaust. Based on these, outlines of the ship geometry and thereby performances are determined. Simple simulations are conducted to assess design feasibility. This is followed by the construction of an accurate digital representation of the geometry using 3D CAD. This 3D model is then passed to CFD for evaluating towing condition, self-propulsion condition, surface flow of the ship, and resistance created by waves. Fluid Techno considers this CFD evaluation process critical. If no problems are detected during this phase, the process moves to designing the propeller, calculating other performance parameters, and conducting experiments. The experiments are usually done only for one model. If problems are detected in this phase, re-designing is performed, but that usually leads to a loss of another half a year which also requires additional cost for physical testing. The completion of all possible preliminary performance evaluations is essential to prevent this. “The time has put CFD at the forefront of today’s alternative means of evaluation,” says Mr. Tamashima. To further promote CFD applications, Fluid Techno collaborated with Software Cradle to introduce SC/Tetra to in-house engineers.
To reduce fuel usage, the hull shape must be constructed to minimize resistance caused by the water. The hull shape must also be adequate for loading cargo. The best shape is determined by balancing all the requirements. To help determine the best design, fluid dynamics technologies are needed. “Major shipbuilders have technical departments specialized for this, but small firms don’t even have such divisions. It takes years of experience to gain proficiency in this field. This is where we can offer our expertise,” says Mr. Tamashima. Fluid Techno conducts CFD evaluations to determine the best shape, which can then be used for the large scale tank test.
CFD for Above Water and Inside Ship
In addition to using simulation to optimize fuel efficiency while satisfying the other ship design requirements, Fluid Techno has keen interests in investigating other issues using SC/Tetra. One of them is worsened maneuverability with increasing ship speed. Conventional CFD tools can be used to analyze resistance caused by water, but they cannot analyze maneuverability thoroughly. SC/Tetra is a candidate tool to verify it (Figure 3).
Figure 3: Analysis results of evaluating the condition shown in Figure 2 using SC/Tetra
Force acting on rudder is verified by changing the size of rudder valve and visualizing the flow.
While Fluid Techno mainly analyzes the section of the ship that is underwater, they also intend to investigate wind pressure resistance above the water surface, which their clients have been requesting. They will evaluate how to reduce wind pressure resistance by altering structure shape.
The ship-related flows include not only external flows around the ship but also internal flows within the ship. For example, the engine cooling system takes in sea water from sea chests located at the bottom of the ship. Fluid Techno is proceeding with verification of SC/Tetra for simulating the ingestion of sea water (Figure 4).
Figure 4 Analysis of sea chest
The use of energy saving devices is another key approach for further improving fuel efficiency. Fuel efficiency could be improved even further by installing these devices in addition to the improved hull shape. Fluid Techno expects to undertake all these evaluations with SC/Tetra.
Fluid Techno is currently calibrating their simulation inputs. “Using experimental data, we are now establishing methods of mesh generation, number of mesh elements generated, and numerical value for tuning. Hopefully this will encourage applications of CFD,” says Mr. Tamada.
The goal of using CFD is to evaluate flow phenomena related to ships across the board. This includes external and internal flows for both water and air. “We are aiming to figure out these types of flows early in the design phase. Our ultimate objective is to come up with the best design in shortest amount of time possible. We expect that CFD will be of great use for achieving this. Through providing our experimental data and improving CFD applications with Software Cradle, the simulation environment will advance drastically,” says Mr. Tamashima.
Easy-to-use Tool with High Quality Postprocessor Capability
Mr. Tamada says: “We found Software Cradle products easy to use. Support engineers of Software Cradle certainly stand ready in doing everything possible to support us. The user reference is well documented for us to understand.”
Fluid Techno finds that mesh generation using SC/Tetra is easy and robust compared to other tools, which, often times, produced errors. They are now working to determine the ideal settings in SC/Tetra for generating mesh elements and mesh refinement. They still want higher calculation speed out of the software although they are facilitating more powerful hardware for that purpose at the same time.
Setting up the SC/Tetra postprocessor to view simulation results is very simple. Results can be easily visualized in many different ways. “SC/Tetra is well-developed software from the aspect of visualization capability,” says Mr. Tamada. He recommends enhancing the report output function to make it even more useful. The future challenge is to analyze vessel performance on waves.
Easier Verification Process
So far, Fluid Techno has completed thorough verification of only rudder capability. “Verification was easy as I imagined.” Mr. Tamashima says, noting that relative differences were clearly identified. “The verification process became much easier and effectively faster.” says Mr. Tamashima. Performing analyses helped them plan better for experiments. “If we didn’t have CFD, we would have to run five experiment cases. But with CFD, we would be able to reduce the number of test cases. It would be possible to allocate experiments of other topics for the place of the eliminated cases instead. Without a doubt, if CFD is incorporated into the ship hull design process, the overall work flow will be much more efficient,” says Mr. Tamashima.
In their continual pursuit of better design, Fluid Techno is always looking to implement new approaches. While they have been designing and performing analyses in three dimensions, viewing models and analysis results has been limited to two dimensions using graphics monitors and paper. As an alternative, Fluid Techno is planning on extending the application of 3D printers. “Some details are difficult to grasp in two dimensional plans, but these can be intuitively evaluated when converted to three dimensional models. The shape of the ship stern is especially important. We are planning to use a three dimensional models for its evaluations,” says Mr. Tamashima. Fluid Techno expect to improve the certainty of the model ship experiments by adding an evaluation process using 3D printers between the CFD analysis phase and model ship experiments.
Fluid Techno has actively implemented 3D applications to elevate their competitiveness. Software Cradle will continue to support their design development.
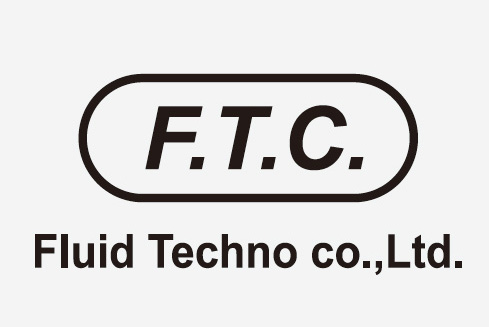
FLUID TECHNO Co., Ltd
- Founded: 2001
- Business: Provides ship design and development support including model ship designs for experiments, test services for ship experiments, and software programs for calculating ship performance. Provides design and implementation services for ship energy saving devices.
- Head Office: 6F Gibraltar Seimei Bldg., Tokiwa-cho, Sasebo, Nagasaki Japan
- Representative: Masahiro Tamashima, President
*All product and service names mentioned are registered trademarks or trademarks of their respective companies.
*Contents and specifications of products are as of February 29, 2016 and subject to change without notice. We shall not be held liable for any errors in figures and pictures, or any typographical errors.
Download